Otimizar o fluxo de pós na hidrometalurgia: desafios, boas práticas e casos de aplicação industrial
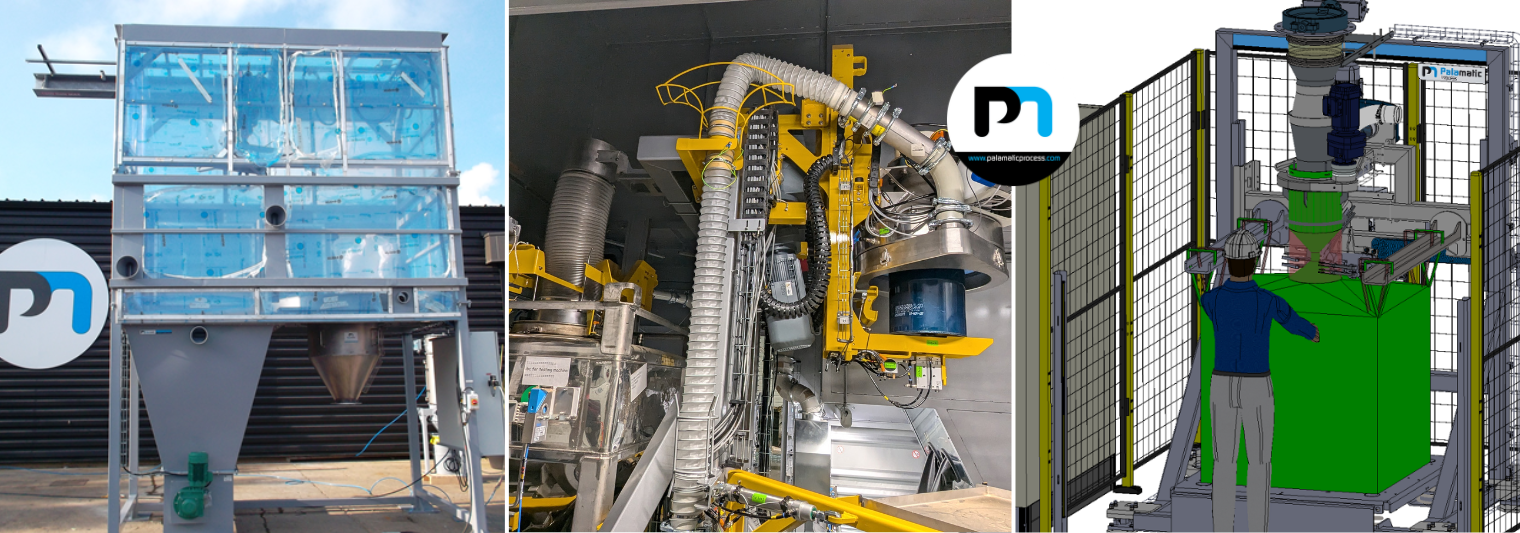
No moderno setor hidrometalúrgico, o controle das propriedades de fluxo dos pós é um grande desafio técnico e econômico.
Os processos hidrometalúrgicos envolvem o manuseio de materiais em pó em vários estágios: moagem de minérios, manuseio de precipitados, filtragem, secagem e embalagem de produtos acabados.
A fluidez inadequada do pó transforma rapidamente uma instalação de alto desempenho em um pesadelo operacional, com o entupimento de silos, formação de abóbadas, segregação de partículas e entupimento de equipamentos.
Este artigo apresenta uma visão geral abrangente dos problemas, métodos e inovações para melhorar a fluidez do pó em processos hidrometalúrgicos a longo prazo.
1. Os desafios técnicos e econômicos dos pós de baixa fluidez
Impact sur les coûts de maintenance
La manipulation de poudres à faible fluidité entraîne une usure prématurée des équipements de transfert.
Les problèmes d'écoulement sont responsables de 35 à 40% des interventions de maintenance non-programmées dans les unités hydrométallurgiques.
Une étude menée en 2023 sur quinze sites de production a démontré qu'une amélioration de l'indice de fluidité des poudres (mesuré par l'angle de repos) de seulement 5° peut réduire les coûts de maintenance associés de 22% en moyenne.
Les composants les plus affectés sont généralement :
- Les vis sans fin et transporteurs, dont la durée de vie peut être réduite de 30 à 50%
- Les vannes et clapets, qui subissent une abrasion accélérée
- Les revêtements intérieurs des silos et trémies, détériorés par les efforts excessifs
Ces défaillances récurrentes conduisent à des dépenses directes (remplacement de pièces, main d'œuvre) estimées entre 2 et 4% du chiffre d'affaires annuel selon la taille des installations.
Pertes de production associées
Les perturbations d'écoulement engendrent des arrêts de production particulièrement préjudiciables.
Une analyse comparative menée sur le secteur hydrométallurgique canadien en 2022 a révélé que les problèmes de fluidité des poudres étaient responsables de :
- 7 à 12% des temps d'arrêt imprévus
- 3 à 5% de réduction du taux d'utilisation global des capacités
- Un manque à gagner moyen de 850€ par tonne de capacité installée et par an
Dans les unités de lixiviation où la régularité d'alimentation en réactifs solides est critique, les fluctuations d'écoulement peuvent réduire les rendements d'extraction métallique de 3 à 8 points, impactant directement la rentabilité.
Incidence sur la qualité des produits
La qualité des produits est fortement tributaire d'un écoulement homogène et contrôlé des poudres.
Les anomalies d'écoulement induisent :
- Des phénomènes de ségrégation : Les particules de tailles ou densités différentes tendent à se séparer lors de l'écoulement, créant des hétérogénéités dans les mélanges.
Dans les procédés de précipitation sélective, cette ségrégation peut induire des variations de pureté du produit final de l'ordre de 0,5 à 2%.
- Des irrégularités de dosage : Un écoulement erratique conduit à des fluctuations de débit pouvant atteindre ±15% autour de la valeur nominale, compromettant la stœchiométrie des réactions et affectant le rendement global.
- Des modifications de propriétés physiques : Les contraintes mécaniques excessives appliquées peuvent altérer la structure cristalline et la morphologie des particules.
Une étude sur les poudres d'oxyde de zinc a démontré que les contraintes de cisaillement élevées pouvaient réduire la surface spécifique jusqu'à 18%, affectant directement la réactivité du produit.
Les non-conformités résultant de ces problèmes représentent en moyenne 2,8% de la production totale dans le secteur.
Risques pour la sécurité industrielle
Les risques liés à une mauvaise fluidité des poudres concernent également la sécurité :
Les risques liés à une mauvaise fluidité peuvent inclure :
- Risque d'effondrement de voûtes : La formation de ponts et voûtes dans les silos crée des zones de vide qui peuvent s'effondrer brutalement, générant des surcharges instantanées.
- Émissions de poussières : Les interventions manuelles pour débloquer les écoulements provoquent des émissions de poussières potentiellement toxiques, représentant un risque d'exposition professionnelle significatif.
- Surcharges mécaniques : Les efforts déployés pour rétablir l'écoulement peuvent soumettre les structures à des contraintes excédant leurs limites de conception.
Les statistiques sectorielles indiquent que 12% des accidents industriels graves dans le domaine hydrométallurgique sont liés à des problèmes d'écoulement de matières solides.
L'analyse des incidents montre que le temps d'exposition des opérateurs aux risques liés aux interventions sur poudres bloquées peut être réduit de 78% par l'amélioration préventive de la fluidité des matériaux.
2. Otimização do tamanho e da morfologia das partículas
Mecanismo de ação
A distribuição e o formato do tamanho das partículas influenciam diretamente as interações entre as partículas e, portanto, a fluidez geral.
A otimização consiste em :
- Ajustar a distribuição do tamanho das partículas para minimizar os espaços intersticiais e, ao mesmo tempo, limitar as forças de coesão
- Favorecer morfologias esféricas ou elipsoidais que reduzam os bloqueios mecânicos e as superfícies de contato.
Essas modificações têm um efeito direto sobre o coeficiente de atrito interno e oângulo natural de repouso, que são parâmetros fundamentais para a fluidez.
Vantagens e limitações
Vantagens:
- Solução de longa duração que não requer aditivos químicos
- Melhoria simultânea da compactação e da fluidez
- Redução significativa do arqueamento (até 65%, dependendo do caso estudado)
Limitações:
- Requer equipamento de moagem/peneiramento preciso e bem conservado
- Pode modificar outras propriedades físico-químicas do material (reatividade, solubilidade)
- O investimento inicial costuma ser substancial
Exemplo industrial
A refinaria hidrometalúrgica de Kokkola (Finlândia) otimizou a distribuição do tamanho das partículas de seu hidróxido de zinco precipitado adotando um sistema de classificação pneumática de duplo estágio.
A distribuição mais rigorosa do tamanho das partículas (90% das partículas entre 45 e 75 μm) resultou em uma melhoria noíndice de fluxo de Hausner de 1,38 para 1,22.
Resultados obtidos:
- 82% de redução nas operações de desbloqueio
- Aumento de 7,3% na taxa de fluxo de massa em sistemas de transferência
- Retorno do investimento obtido em 8,5 meses de operação
- Economia anual estimada de €420.000
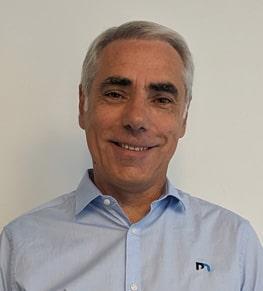
Você tem um projeto em mente?
Estou aqui para aconselhá-lo e ajudá-lo com seu projeto.
Orlando, especialista em manuseio de pós em processos industriais
3. Soluções operacionais para melhorar a fluidez do pó
Adição de aditivos fluidificantes
Mecanismo de ação
Os aditivos fluidificantes atuam por meio de três mecanismos principais:
- Redução das forças eletrostáticas pela neutralização das cargas superficiais
- Redução das forças de Van der Waals por meio da modificação da rugosidade da superfície
- Criação de uma camada limite que reduz o contato direto entre as partículas.
Os aditivos mais comumente usados na hidrometalurgia são a sílica pirogênica (0,1-0,5%), os estearatos metálicos (0,2-1%) e determinados derivados orgânicos, como o polietilenoglicol (0,3-0,8%).
Vantagens e limitações
Vantagens:
- Rápido de usar sem grandes modificações no equipamento
- A dosagem pode ser ajustada para se adequar às condições operacionais
- Alta eficiência mesmo em baixas concentrações (normalmente <1%)
Limitações
- Custo recorrente do consumo de aditivos
- Risco de contaminação do produto final
- Compatibilidade às vezes limitada com as etapas subsequentes do processo
Exemplo industrial
Em uma unidade de produção de óxido de cobre a partir de lixiviados no Chile, a incorporação de 0,3% de sílica pirogênica hidrofóbica no pó de óxido após a filtração permitiu
- Uma redução no ângulo de repouso dinâmico de 56° para 38°.
- Uma redução de 91% nos bloqueios em sistemas de ensacamento
- Maior precisão na dosagem, de ±12% para ±3
- Um custo adicional de material de € 1,2/tonelada compensado por uma redução nos custos operacionais de € 3,8/tonelada
O uso de um aditivo de origem biológica baseado em amido modificado (0,4%) mostrou eficácia comparável com uma redução de 43% no impacto ambiental, de acordo com a análise do ciclo de vida.
Tratamentos mecânicos específicos
Mecanismo de ação
Os tratamentos mecânicos têm como objetivo romper as forças de coesão entre as partículas e fornecer a energia necessária para iniciar e manter o fluxo.
São usadas três abordagens principais:
- Vibração controlada: aplicação de vibrações de frequência e amplitude otimizadas para fluidizar temporariamente a massa de pó sem induzir à compactação.
- Fluidização mecânica: uso de agitadores, misturadores ou discos rotativos para criar um cisalhamento controlado que mantém o pó em um estado quase fluido.
- Assistência pneumática: injeção de ar a baixa pressão para reduzir o contato entre as partículas e facilitar o fluxo.
Vantagens e limitações
Vantagens:
- Ação imediata no fluxo
- Adaptabilidade a variações nas propriedades do material
- Preservação das características físico-químicas do pó
Limitações :
- O consumo de energia pode ser alto
- Possível atrito de partículas frágeis
- Projeto específico necessário para cada instalação
Exemplo industrial
A Umicore implementou um sistema de fluidização mecânica usando um cone vibratório em sua unidade de tratamento de lodo anódico em Hoboken (Bélgica).
O sistema combina vibração de baixa frequência (12 Hz) com injeção de ar pulsado sincronizado.
Os resultados falam por si:
- Aumento da taxa de fluxo de 760 kg/h para 1250 kg/h (+64%)
- Redução da variabilidade da taxa de fluxo de ±18% para ±4
- Redução do consumo de energia por tonelada transferida de 1,8 kWh para 1,2 kWh
- Eliminação completa da intervenção manual para desbloqueio
O investimento de 175.000 euros se pagou em menos de 14 meses, graças aos ganhos de produtividade e à redução dos custos de manutenção.
Mudanças nas condições ambientais
Mecanismo de ação
As propriedades de fluxo dos pós são fortemente influenciadas pelas condições ambientais:
- Controle da umidade relativa: a redução da umidade limita a formação de pontes líquidas entre as partículas, um fenômeno que é particularmente problemático para os sais de umidade.
- Gerenciamento da temperatura: um aumento controlado da temperatura reduz a adsorção de umidade e pode reduzir as forças de adesão entre as partículas.
- Modificação da pressão: em alguns casos, uma leve pressurização ou despressurização pode melhorar significativamente as características do fluxo.
Vantagens e limitações
Vantagens:
- Melhoria uniforme nas propriedades de fluxo
- Sem alteração química dos produtos
- Possível sinergia com outros métodos de otimização
Limitações :
- Custos de energia associados ao ar condicionado
- Complexidade técnica dos sistemas de controle ambiental
- Sensibilidade a variações sazonais
Exemplo industrial
Uma fábrica de produção de sulfato de níquel na Austrália implementou um sistema de controle ambiental integrado para suas unidades de secagem e condicionamento.
O sistema mantém uma umidade relativa inferior a 35% e uma temperatura constante de 33°C nas áreas críticas de transferência de pó.
Os resultados documentados após 12 meses de operação são significativos:
- Melhoria noíndice de fluidez de Carr de 22 para 16
- Redução de 68% nos incidentes de fluxo
- Perdas de produto relacionadas ao manuseioreduzidas de 2,3% para 0,8
- Consumo adicional deenergia de 135 kWh/tonelada compensado por um aumento de 11% na produtividade
4. Inovações tecnológicas recentes e perspectivas futuras
Revestimentos nanoestruturados
Revestimentos de polímero ou cerâmica em nanoescala são agora aplicados a superfícies em contato com pós.
Esses tratamentos criam padrões de superfície otimizados (tipo “pele de tubarão”) que reduzem drasticamentea adesão das partículas.
Os testes industriais mostram uma redução noângulo de atrito de 30 a 40% em comparação com as superfícies polidas convencionais.
A durabilidade desses revestimentos agora chega a 18 a 24 meses em ambientes abrasivos.
Sistemas de caracterização on-line
A reologia do pó agora pode ser monitorada continuamente usando sensores acústicos e ópticos não intrusivos.
Esses sistemas analisam em tempo real
- Distribuição do tamanho das partículas
- Coesão entre partículas
- Tendências de aglomeração
Juntamente com algoritmos de inteligência artificial, esses sistemas permitemprever problemas de fluxo e ajustar automaticamente os parâmetros operacionais antes que ocorram bloqueios.
Fluidização eletrostática controlada
Uma abordagem inovadora envolve a aplicação de um campo eletrostático modulado que modifica as forças de coesão entre as partículas.
Os protótipos atuais permitem que as forças de adesão sejam reduzidas em até 60% sem modificação química do pó.
Essa tecnologia, que ainda está em fase de demonstração industrial, parece particularmente promissora para pós metálicos finos e óxidos semicondutores.
Bioaditivos da economia circular
Pesquisas recentes identificaram vários subprodutos agrícolas e florestais que, após tratamento específico, têm excelentes propriedades de fluidização.
Esses aditivos de base biológica oferecem uma alternativa sustentável aos agentes de fluxo sintéticos, com um impacto ambiental reduzido em 70 a 85%.
Os derivados de lignina modificados e as nanofibrilas de celulose apresentam desempenho comparável ao das sílicas pirogênicas convencionais em concentrações equivalentes.
Conclusão
Conclusão
A otimização da fluidez do pó é uma alavanca de desempenho crucial para osetor hidrometalúrgico.
Para os fabricantes que desejam aprimorar seus processos, recomendamos :
- Caracterização precisa das propriedades de fluxo dos pós em cada estágio crítico do processo
- O desenvolvimento de uma estratégia integrada que combine otimização do tamanho das partículas, aditivos e assistência mecânica adequada
- Instalar sistemas de monitoramento para detectar desvios em um estágio inicial e tomar medidas preventivas
- Treinar as equipes operacionais nos fundamentos da mecânica dos pós
- Integrar a fluidez como um parâmetro fundamental no processo demelhoria contínua
O retorno do investimento, geralmente inferior a 18 meses, combinado com a melhoria das condições de trabalho e da qualidade do produto, justifica plenamente a crescente atenção dada a essa questão pelos líderes do setor hidrometalúrgico.
Você trabalha com processamento ou beneficiamento dehidrometalurgia?
Entre em contato com nossos especialistas para projetarmos juntos uma linha de produção personalizada, de alto desempenho e segura.