Muitas vezes há confusão entre os termos rosca transportadora, rosca alimentadora, esteira vibratória e alimentadora vibratória. Neste artigo vamos definir o que é exatamente o equipamento de dosagem de pó e como escolher o melhor tipo de equipamento para seus materiais entre um dosador de rosca e um dosador vibratório.
1. Principais funções de um equipamento de dosagem
O equipamento de alimentação não é um sistema de transporte. Transportadores mecânicos, tais como roscas transportadoras (também conhecidas como roscas transportadoras) e transportadores vibratórios, geralmente consistem de uma entrada e uma saída com a única finalidade de mover material do ponto A para o ponto B em longas distâncias. Eles normalmente operam a uma taxa fixa e movem o material para jusante a uma taxa constante medida em toneladas ou quilogramas por hora.
O equipamento de dosagem é usado em situações onde é necessário um maior controle e precisão do fluxo de material. Alimentadores de rosca e alimentadores vibratórios não são usados para mover material por longas distâncias, mas sim para dosar material de um funil ou IBC para uma linha de embalagem ou um triturador industrial. Eles são muito menores que os transportadores mecânicos e consistem de um funil integrado, um agitador, um pequeno tubo ou base plana e um acionamento de freqüência variável.
A tremonha integrada é necessária para a dosagem do equipamento, pois uma carga de cabeça constante deve ser mantida para o funcionamento adequado. A velocidade pode ser controlada no equipamento de alimentação através de uma VFD para permitir velocidades de alimentação mais lentas ou mais rápidas.
Se seu processo exige a reembalagem do material processado em sacos de papel de 25-50kg e você precisa ter certeza de não sobrecarregar ou subcarregar o recipiente, um alimentador é a resposta. Da mesma forma, os moinhos de pó têm melhor desempenho quando operam a uma taxa de alimentação constante e consistente.
2. Considere as características de seu material
Pós e grânulos podem ter propriedades diferentes que afetarão muito seu comportamento em um processo de fabricação. Portanto, é importante estudar estas características antes de selecionar seu equipamento industrial. Em geral, os seguintes são os atributos comuns a serem analisados para materiais a granel:
- Higroscopicidade: Açúcar, sal e certos tipos de pós químicos podem absorver fácil e prontamente a umidade da atmosfera ao redor, o que pode fazer com que o material se aglomere e endureça durante períodos prolongados de armazenamento e repouso.
- Aeração: Contas de vidro, farinha e resinas freqüentemente têm um ângulo baixo de repouso e se comportam como um fluido quando arejadas. Este material pode facilmente inundar (fluxo incontrolável) processos a jusante se não for controlado.
- Agrupamento: A farinha de madeira ou fibras de biomassa e similares contêm partículas longas que se aglomeram e formam massas que podem bloquear os canais de fluxo.
- Adesão: Materiais tais como pigmentos em pó podem ser adesivos, ou seja, colar e agarrar-se a qualquer superfície imaginável, o que pode tornar este tipo de produto muito difícil de manusear.
- Friabilidade: Pastas, flocos ou alguns produtos granulados podem ser facilmente quebrados (o chamado atrito) se manuseados de forma muito grosseira. Por este motivo, são necessários equipamentos capazes de manusear e transferir o material suavemente para manter a integridade do produto.
- Facilidade de fluxo: As pelotas plásticas fluem facilmente por gravidade, com pouca ou nenhuma ajuda de fluxo ou equipamento especialmente projetado.
- Abrasividade: Pós de vidro, cimento Portland, etc. podem ter propriedades que desgastam os componentes do equipamento rapidamente se seu processo não for projetado com esta característica em mente. Isto pode levar a manutenção freqüente e dispendiosa.
Antecipar como seu pó se comportará é, portanto, um passo fundamental na escolha de seu equipamento de dosagem.
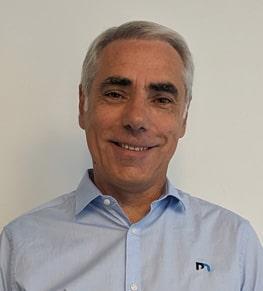
Você não tem certeza sobre qual tipo de unidade de dosagem
selecionar? Estou disponível para discutir e aconselhá-lo.
Orlando, especialista em pó
3. Diferenças em desempenho e design
Os alimentadores de rosca utilizam um funil integrado com um agitador que alimenta um canal tubular. Dentro do tubo há um pequeno parafuso que empurra o produto através de uma saída para o processo downstream. Há vários projetos para o pequeno parafuso nos alimentadores de rosca: parafusos de rabo de porco, parafusos de fita e parafusos com um eixo de acionamento.
- Os parafusos de rabo de porco não têm eixo central e são freqüentemente utilizados para materiais que têm as seguintes características: densidade leve e/ou são pegajosos ou coesivosos. Exemplos: farinha, cacau em pó e óxidos.
- Os parafusos de fita têm um eixo central, mas as asas estão abertas e conectadas ao eixo em um ponto. Os parafusos de fita são utilizados em materiais leves e granulados, como PVC e granulados de polímero.
- Os parafusos de eixo central são utilizados para materiais mais densos ou de fluxo livre, tais como pós metálicos.
Os dosadores de rosca oferecem boa precisão. Em alguns casos, a precisão da dosagem é de -/+ 1-2 gramas. Este é o tipo de alimentador mais comumente utilizado, pois é adequado para a maioria das aplicações, exceto no caso de materiais frágeis ou sensíveis ao calor.
Os dosadores vibratórios têm uma estrutura similar (funil e unidade de estrutura tubular), mas em vez de um parafuso, motores de agitação são acoplados à unidade e a estrutura é apoiada por molas, para permitir que a unidade vibre. Um ângulo muito pequeno permite que a unidade mova o material ao longo do leito de alimentação para o processo a jusante. A taxa de alimentação pode ser controlada aumentando ou diminuindo a amplitude e a freqüência das vibrações. A agitação mantém a integridade do material ou evita desgaste desnecessário no caso de materiais abrasivos. Portanto, quando se trata de materiais friáveis, sensíveis à temperatura ou abrasivos, os alimentadores vibratórios são a solução ideal.
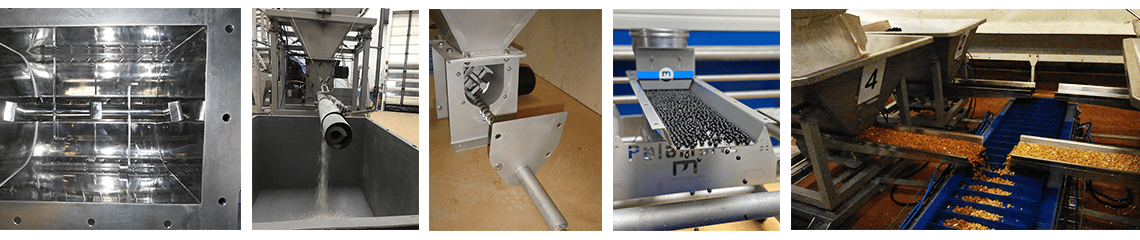
4. Vantagens e desvantagens das roscas alimentadoras e dos alimentadores vibratórios
Dosador de rosca
Principais vantagens de um dosador de rosca:
- Os tipos de parafusos podem ser variados e facilmente intercambiáveis para atender a uma grande variedade de pós
- O parafuso proporciona extração positiva (tração) do funil
- Pode ser projetado para aplicações fáceis de limpar, sem a necessidade de remover a unidade inteira da linha
Principais desvantagens de um dosador de rosca:
- Materiais adesivos e multas podem se acumular no interior do material, limitando a produção
- Peças móveis podem causar desgaste adicional no equipamento, resultando em maiores exigências de manutenção
- Consome mais energia do que um alimentador vibratório
Dosador vibratório
Principais vantagens de um dosador vibratório:
- O comedouro trabalha tanto com taxas de alimentação baixas quanto altas
- Produz um fluxo de material uniforme para um manuseio suave
- Praticamente sem peças móveis, reduzindo os requisitos de manutenção
- Baixo consumo de energia
Principais desvantagens de um alimentador vibratório:
- A ação vibratória pode gerar pó com alguns pós finos
- A vibração pode potencialmente separar materiais que tenham sido misturados
- Não fornece extração positiva (um meio de puxar o material do funil)
- Material pegajoso ou multas podem se acumular na bandeja de alimentação, limitando a produção